- Szczegóły
- Opublikowano: wtorek, 29 marzec 2022 08:15
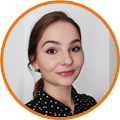
Marta Soczyńska
Odpowiada za dział marketingu i dokłada swoją cegiełkę w sprzedaży produktów firmy Profesal.
Prewencja a predykcja w utrzymaniu ruchu.
Zmniejszenie strat przedsiębiorstwa wynikających z przestojów.Zwiększenie produktywności parku maszynowego.
Utrzymanie wysokiego poziomu niezawodności infrastruktury technicznej.
Brzmi jak ideał parku maszynowego, który pracuje niezawodnie, bez konieczności rozwiązywania zgłoszeń awarii czy usterek. Niestety rzeczywistość często bywa zupełnie inna. Kłopoty z maszynami i narzędziami wykorzystywanymi przez pracowników, to naturalna kolej rzeczy przy intensywnej eksploatacji urządzeń. Są jednak rozwiązania, które pomagają minimalizować czas napraw i ich występowanie.
W dzisiejszym artykule przedstawimy Państwu kilka z nich!
Niezawodność maszyn może wzrosnąć.
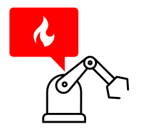
Wyobraźmy sobie, że na maszynie nastąpiła awaria.
Rozwiązywanie problemu powinno nastąpić niezwłocznie, żeby ograniczyć koszty przestoju. Jednak w przypadku, gdy następuje problem w trakcie serwisu, wynikający z niewiedzy jak powinno się go poprawnie wykonać, zwiększa się koszt naprawy.
Służby Utrzymania Ruchu zauważając problemy, z biegiem czasu wyznaczyła trzy główne strategie UR:
- reakcyjne utrzymanie ruchu (ang. reactive maintenance),
- prewencyjne utrzymanie ruchu (ang. preventive maintenance),
- predykcyjne utrzymanie ruchu (ang. predictive maintenance).
Początkowym modelem działania utrzymania ruchu było reagowanie reakcyjne, polegające na odpowiedzi na zaistniałą usterkę czy awarię w momencie, gdy ona nastąpiła.
„O, zepsuło się? Spokojnie, naprawimy to!”.
Następnie zaczęto obserwować powtarzalność niektórych awarii, jednak wydłużający się czas jej napraw, wynikał z braku konkretnego rozwiązania, które za każdym razem było wymyślane przez nowych pracowników, a ewentualne poznanie go wymagało kontaktu z przełożonym lub bardziej doświadczonym pracownikiem zespołu. Wprowadzono więc model prewencyjnego UR. Polega on na gromadzeniu dokumentacji, informacji potrzebnych do wykonania powtarzających się napraw. Dzięki łatwemu dostępowi do odpowiednich danych, technicy mogą błyskawicznie zorientować się w zaistniałej sytuacji i dokonać napraw szybciej i efektywnej. A na tym nam zależy. ?
Najbardziej zaawansowana strategia UR wymaga najwięcej nakładów pracy i finansów. Żeby móc zastosować działania predykcyjne, musimy być w stanie przewidzieć awaryjność maszyn, w czym pomagają wskaźniki takie jak:
- MTTR – średni czas naprawy (ang. Mean Time To Repair),
- MTTF – średni czas do uszkodzenia, występuje w przypadku elementów nienaprawialnych (ang. Mean Time To Failure),
- MTBF – średni czas pomiędzy naprawami (ang. Mean Time Between Failure),
- Dostępność techniczna maszyn.
Monitorowanie i analiza tych wskaźników pozwala trafnie ocenić czas, by zaplanować przeglądy i działania konserwacyjne. Pomagają w tym czujniki zamontowane na maszynach, które w czasie rzeczywistym, przekazują informacje o stanie zasobu. Dzięki ich zastosowaniu możemy wcześniej wykryć drobne nieprawidłowości jakich nie widać „gołym okiem”, które mogą prowadzić do wystąpienia awarii. Przydatna jest oczywiście wcześniej zgromadzona dokumentacja poszczególnych maszyn, która pomaga w działaniach naprawczych. Warto zapamiętać, że taka strategia pozwala reagować, jeszcze przed wystąpieniem awarii, co znacząco zmniejsza koszty, które musielibyśmy przeznaczyć na przywrócenie maszyny do prawidłowego stanu technicznego. Dodatkowymi korzyściami wynikającymi z wprowadzenia działań predykcyjnych to wydłużenie żywotności maszyn i zapewnienie ciągłości ich pracy.
Czujniki na maszynie? Komu to potrzebne?
Przemysłowy Internet Rzeczy to jedna z wiodących technologii w ewolucji cyfrowej. Założenia jakie ze sobą niesie to zwiększenie automatyzacji i komunikacji, przy użyciu sztucznej inteligencji, nowych technologii i wciąż rozwijających możliwości. Czujniki pobierające dane z maszyn to cenne narzędzia, ułatwiające sprostać założeniom IIoT (ang. Industrial Internet of Things).
Jednak jakie konkretnie dane, możemy pobierać z tego typu urządzeń, jak odczytują one wskaźniki i jakie rodzaje czujników możemy wyróżnić? Klasyfikacja czujników rozgałęzia się na czujniki analogowe i cyfrowe, mechaniczne i elektryczne, a w zasadzie podziały można tak tworzyć i tworzyć… Ze względu na technologię otrzymywania, sposób przetwarzania sygnałów i wiele innych wedle uznania… ? Nie zagłębiając się jednak w metody działania i reakcje fizyczne, jakie dzięki nim zachodzą, możemy zwrócić uwagę na parametry jakie mogą mierzyć, w tym:
- temperatura,
- ciśnienie,
- drgania
- prędkość lub przyśpieszenie,
- dźwięk i jego natężenie.
A korzyści jakie możemy osiągnąć przy wykorzystaniu czujników, to:
- bezpieczeństwo zespołu
- zwiększenie wydajności i produktywności maszyn,
- przyśpieszenie czasu reakcji na awarię, a z czasem:
- zminimalizowanie liczby występujących awarii,
- zmniejszenie kosztów utrzymania parku maszynowego.
Co pomaga wprowadzić strategię prewencyjną i predykcyjną UR?
Systemy, dzięki którym możemy uzyskać raporty kosztów, listy kontrolne potrzebne do przeglądów czy wskaźniki pobierane z czujników, są dostępne na rynku i zapewniają dostępność wszystkich najważniejszych analiz w jednym miejscu. Istotne jest również gromadzenie historii usterek i napraw, aby dostęp do dokumentacji był szybki i łatwo dostępny.
Możliwości jakie oferują systemy CMMS to również mapowanie maszyn, dzięki czemu, przy wystąpieniu awarii, jesteśmy w stanie błyskawicznie zorientować się, na którym z urządzeń doszło do uszkodzenia, a jeśli spowodowało to zatrzymanie linii – niezwłocznie reagować.
Systemy CMMS pomagają również lepiej zaplanować przeglądy czy konserwacje maszyn, a dzięki możliwości powiadamiania, możesz mieć pewność, że żadne z nich nie zostanie pomięte. Niezależnie od tego czy park maszynowy w twojej firmie liczy 8 czy 80 maszyn, ważne jest by zadbać o działania zapobiegające przestojom. Pamiętaj, że jest to inwestycja, która może zwrócić się szybciej, niż myślisz!