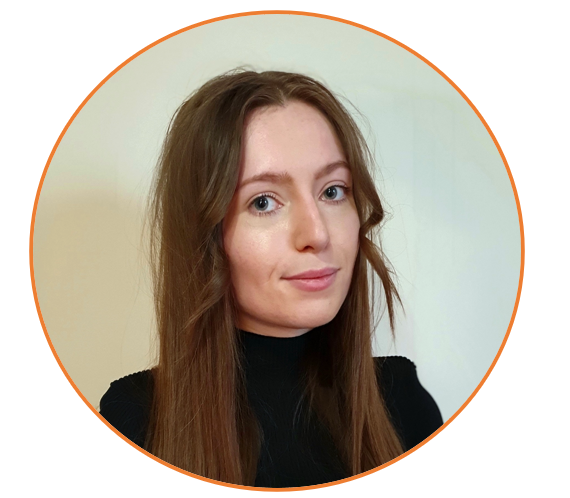
Aleksandra Kamińska
Stażystka w dziale marketingu, przynosi nowe pomysły i świeże spojrzenia na strategię firmy Profesal
Optymalizacja UR za pomocą Lean Tools
Dział Utrzymania Ruchu to jednostka, która ma ogromny wpływ na działanie całego przedsiębiorstwa. To od niej zależy ciągłość produkcji, stan maszyn, planowanie przeglądów czy czas reakcji na pojawiające się usterki oraz awarie. Są to czynniki, które bezpośrednio wpływają na zysk i rozwój firmy. Kierownik Utrzymania Ruchu powinien, więc dążyć do ciągłej optymalizacji i poprawy procesów produkcji tak, aby maksymalnie ułatwić pracę technikom oraz wykluczyć w miarę możliwości czynności, które nie dodają wartości.
W lepszej standaryzacji i optymalizacji procesów Kierownikowi Utrzymania Ruchu może zdecydowanie pomóc Lean Management. Metodologia Lean, najprościej mówiąc, to koncepcja zarządzania, która polega na maksymalizacji wartości dla klienta przy jednoczesnej minimalizacji wszelkich strat i utrzymaniu wysokiej jakości. Więcej o samej idei i założeniach możesz dowiedzieć się więcej w artykule „Co łączy ze sobą skróty Lean, TPM i CMMS?”.
Koncepcja Lean to przede wszystkim masa narzędzi (tzw. Lean Tools), dzięki którym możemy usprawniać procesy i udoskonalać działanie produkcji. W tym artykule przedstawimy najbardziej przydatne narzędzia, które pozwolą na usprawnienie działań produkcji i eliminacje marnotrawstw.
SMED (Single Minute Exchange of Die)
Umiejętnie wykorzystana metodyka SMED pozwala na skrócenie czasu przezbrojeń maszyn i urządzeń poprzez eliminacje wszelkich niepotrzebnych czynności i ich reorganizację. Narzędzie Lean składa się z etapów, które wykonywane dokładnie z pewnością przełożą się na znaczne zaoszczędzenie czasu.
Analiza procesu przezbrojenia
Pierwszym etapem podczas wdrażania SMED jest nagranie całego procesu przezbrojenia. Pozwoli to nie tylko zarejestrować czas poszczególnych czynności, ale także wyłapać zbędne ruchy i poznać ich przyczynę. Ważne jest, aby analiza nagrania odbywała się w zespole składającym się z osób na różnych stanowiskach (np. technolog, operator, kierownik UR, przedstawiciel działu BHP), co daje szerszą perspektywę analizowanych procesów. Należy również przygotować dokument, w którym odznaczymy, ile czasu poświęcono na poszczególne czynności.
Podział procesów na kategorie
W tym etapie kategoryzujemy wszystkie czynności zarejestrowane w poprzednim kroku. Procesy dzielimy na wewnętrzne i zewnętrzne. Wewnętrzne to wszystkie operacje, które są wykonywane, wtedy, gdy maszyna nie pracuje, natomiast zewnętrzne to procesy, które mogą być wykonywane podczas pracy maszyny. Należy wyodrębnić również wszystkie zbędne czynności podczas przezbrojeń typu: oczekiwanie na części, szukanie narzędzi i części, szukanie dokumentacji potrzebnej do przezbrojenia, zastanawianie się.
Reorganizacja czynności
W przedostatniej części należy zastanowić się, które z czynności jesteśmy w stanie przenieść z kategorii wewnętrznej do zewnętrznej, tak aby maksymalnie skrócić czas przezbrojenia maszyny. Po reorganizacji czynności należy wykluczyć wszystkie te operacje, które zaliczają się do marnotrawstw wymienionych powyżej.
Standaryzacja i doskonalenie
W ostatnim etapie należy ustalić pewien standard przezbrojenia danej maszyny. Najlepszym rozwiązaniem jest przygotowanie instrukcji oraz checklists dla nowego ulepszonego procesu przezbrojenia i udostępnić je technikom. Warto również po pewnym czasie znów wykonać nagranie całego przezbrojenia tak, aby porównać go z poprzednim procesem i wyciągnąć z niego konkretne dane i procent poprawy.
5S
Metodyka ta jest często przywoływana w kontekście World Class Manufacturing, ponieważ odwołuje się bezpośrednio do jednego z jego filarów. 5S to podstawowe narzędzie pozwalające na uporządkowanie i standaryzację stanowiska pracy. Jest to wyjątkowo prosta metoda pozwalająca na szybki, widoczny efekt oraz usprawnienie swojej pracy. 5S składa się z pięciu kolejnych kroków, których nazwy rozpoczynają się na literę ’’S’’.
Sortowanie
W pierwszym kroku zastanawiamy się, które z rzeczy na stanowisku są w ogóle nieużywane, rzadko używane i bardzo często używane. To ważny aspekt, aby pozbyć się wszystkich rzeczy, które nie są nam potrzebne do wykonywanej pracy, a jedynie zabierają nam przestrzeń. Jeśli chodzi o rzeczy wyjątkowo rzadko używane, należy zastanowić się nad ich wyrzuceniem lub składowaniem w specjalnie wyznaczonych miejscach.
Systematyka
To etap, w którym staramy się rozplanować stanowisko pracy w taki sposób, żeby każda nowa osoba mogła włatwy sposób się na nim odnaleźć. Warto w konsultacji z pracownikiem zapoznać się z jakich narzędzi korzysta najczęściej, wtedy możemy umieścić je najbliżej, aby były zawsze pod ręką. Ważne jest również podpisanie półek oraz pojemników, tak aby ograniczyć czas na szukaniu danych rzeczy. Częstym sposobem jest także tzw. „tablica cieni”. Jest to tablica z obrysami danych narzędzi potrzebnych na tym stanowisku, dzięki niej możemy szybko stwierdzić brak któregoś z nich oraz przyspieszyć proces szukania.
Sprzątanie
W tym kroku, ważne jest nie tylko posprzątanie stanowiska, ale i również odszukanie przyczyny występowania zanieczyszczeń, ponieważ możliwe, że jesteśmy w stanie im zapobiec. Ponadto należy ustandaryzować proces sprzątania poprzez określenie konkretnych terminów, narzędzi i chemii potrzebnych do tego procesu. Warto również utworzyć instrukcję jak krok po kroku należy daną maszynę czyścić.
Standaryzacja
Przedostatni etap polega na określeniu standardu dla wykonywania poprzednich 3S. Niezwykle ważne jest określenie procedur, jasnych instrukcji czy checklist, dzięki którym nasze działania nie pójdą na marne, a pracownicy będą mogli w łatwiejszy sposób się do nich dostosować.
Samodyscyplina
Krok określany jako najtrudniejszy ze wszystkich etapów 5S. Zakłada on konsekwentność w wykonywaniu określonych wcześniej założeń, aż ostatecznie będziemy mogli mówić o wyuczonym nawyku. Niezbędnym aspektem jest przypisanie konkretnych osób do wykonywania danych zadań. Warto również wprowadzić cykliczne audyty, które pozwolą kontrolować postępy wdrożonych działań.
Kaizen
To koncepcja, której nazwa wywodzi się z dwóch japońskich słów kai – zmiana oraz zen – dobra. Kaizen jest więc koncepcją polegającą na ciągłym doskonaleniu i usprawnianiu. Mówi również o tym, że zmiana powinna zaczynać się od małych kroków. Zmiana jest rzeczą nieuniknioną, ale w myśl idei Kaizen warto dążyć małymi etapami do celu, angażując przy tym pracowników, tak, aby oni sami mogli się powoli przystosowywać.
Warto wprowadzić ideę Kaizen do swojej firmy np. pod względem systemu sugestii. Bardzo często Kierownicy nie zauważają pewnych luk w działaniu produkcji, z którymi na co dzień borykają się technicy. Wprowadzenie systemu, dzięki któremu możemy zbierać pomysły pracowników, może okazać się niezwykle cennym narzędziem usprawniającym działanie produkcji.
W obecnych czasach, gdy cyfryzacja przedsiębiorstwa to podstawowy aspekt prężnego rozwoju firmy warto inwestować w systemy, które działają w myśl ideologii Lean oraz pomagają wprowadzić TPM (Total Productive Maintenance).
Takim systemem jest z pewnością CMMS Profesal Maintenance. Jest to system dedykowany dla działów Utrzymania Ruchu w przedsiębiorstwach produkcyjnych gwarantujący cyfryzację i zwiększenie produktywności SUR.
Przykładowo moduł zgłoszeń Kaizen w naszym systemie polega na możliwości dodania pomysłu przez pracownika w każdej chwili poprzez dedykowany kafelek. W myśl filozofii Kaizen istnieje możliwość automatycznego wygenerowania zadania na podstawie dodanego, rozpatrzonego pomysłu tak, aby od idei do działania była jak najkrótsza droga.
Chcesz wprowadzić w swojej firmie system wspomagający dział UR z elementami Lean Management?
Chcesz poznać więcej szczegółów na temat naszego systemu?