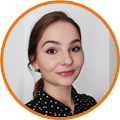
Marta Soczyńska
Odpowiada za dział marketingu i dokłada swoją cegiełkę w sprzedaży produktów firmy Profesal.
Co łączy ze sobą LEAN, TPM i CMMS?
Przemysł obecnie poszukuje narzędzi, aby móc zwiększyć efektywność pracy, zminimalizować koszty i maksymalizować zyski. Istnieje wiele modeli działania, które prowadzą do osiągnięcia wyznaczonego celu, jednak aktualnie najbardziej popularnym jest Lean Manufacturing. Pozwala on osiągnąć wzrost wydajności aż do 66%. Częścią metodyki Lean jest strategia TPM, jednak większość osób nie zdaje sobie sprawy, co tak naprawdę łączy te dwa zagadnienia i gdzie, w procesie wdrażania ich, jest miejsce dla systemów CMMS.
Założenia Lean
Lean w języku angielskim oznacza „szczupły”, koncepcja szczupłego wytwarzania – Lean Manufacturing, została wypracowana w oparciu o system produkcyjny Toyoty, a wdrożenie jej prowadzi nie tylko do zwiększenia wydajności produkcji, ale i całego przedsiębiorstwa (Lean Management).
Czy wiesz, jaka jest pierwsza i najważniejsza kwestia, bez której wprowadzenie metodologii Lean się nie uda? To skupienie na ludziach, postawienie człowieka ponad narzędzia. Aby efektywnie i rozważnie przeprowadzać zmiany w swoim przedsiębiorstwie, musisz dbać o edukację pracowników. Bez zaangażowania pracowników każdego szczebla zoptymalizowanie produkcji nie będzie możliwe.
Kolejnym wyróżnikiem kultury Lean jest skupienie na niwelowaniu marnotrawstwa. Operacje wykonywane w przedsiębiorstwie, związane z produkcją, możemy podzielić na te, które przynoszą wartość oraz te, które nie przynoszą wartości (Muda z jap. marnotrawstwo). Wyróżnia się 7 podstawowych strat (Muda), najlepiej obrazujących pojęcie marnotrawstwa:
- Nadprodukcja – produkowanie za wcześnie, więcej niż potrzeba, powoduje zużycie surowców wcześniej niż jest to potrzebne, niepotrzebny wkład siły roboczej, maszyn oraz urządzeń. Występuje przy tym problem magazynowania wytworzonych towarów. Nadprodukcja to najniebezpieczniejsze marnotrawstwo z siedmiu, ponieważ powoduje ono pozostałe straty. Jeśli wyeliminujemy nadprodukcję, inne marnotrawstwa również znikną.
- Zapasy – niepotrzebne gromadzenie produktów, półfabrykatów czy części powoduje niepotrzebne zajęcie przestrzeni, wyposażenia (wózków, koszów), siły roboczej, która musi zająć się administrowaniem, zarządzaniem zapasami.
- Braki – wytwarzanie produktów, które nie spełniają wymagań klientów, wymagające poprawek, pochłania czas i materiały, co generuje dodatkowe koszty.
- Zbędny ruch – zbędne ruchy pracowników, nieprzynoszące wartości, marnują czas, utrudniają proces produkcyjny oraz zwiększają prawdopodobieństwo wystąpienie wypadków. W wyeliminowaniu tego marnotrawstwa pomaga metoda 5S (5 kroków) – reorganizacja miejsca pracy, przeorganizowanie stanowisk i procesów.
- Zbędne przetwarzanie – zbyt długa praca maszyny powoduje jej szybkie zużycie i wzrasta prawdopodobieństwo wystąpienia usterek. Przyczyną mogą być nieadekwatne technologie i projekty, nieodpowiednia synchronizacja procesów oraz czynności wykonywanych w ich obrębie.
- Oczekiwanie – momenty, w których pracownik czeka bezczynnie, aby móc zacząć wykonywać zadanie, wywołane niewłaściwym zbalansowaniem linii produkcyjnej, brakiem niezbędnych części, awariami maszyn. Skutkami jest między innymi zbyt długi czas produkcji, niedotrzymanie terminów.
- Transport – nadmiarowy transport, nieprzynoszący wartości, powoduje marnotrawstwo czasu i przestrzeni hali produkcyjnej, nie wspominając o fakcie, że może w jego trakcie dojść do uszkodzeń i wypadków.
Jak radzić sobie z występowaniem marnotrawstwa? Narzędzia takie jak: tablice Kanban – dzięki możliwości przejrzystego wglądu w prace zaplanowane, w toku i ukończone, pozwalają lepiej organizować czas i miejsce pracy zespołów, VSM - Value Stream Mapping – to rodzaj analizy aktualnych procesów mających wartość dla klienta, której celem jest usprawnienie przepływu wartości w organizacji. W tym celu wykorzystuje się mapowanie procesu produkcyjnego, dzięki czemu poznajemy dokładnie każdy etap przepływu, co pozwala dostrzec miejsca, w których strumień jest zaburzony; Kaizen – jako filozofia „zmiany na lepsze”, skupia się na ciągłym doskonaleniu działania przedsiębiorstwa. Poszukiwanie i wprowadzenie nawet najmniejszych zmian, przybliża nas do osiągnięcia celu metodą małych kroczków.
Wśród głównych założeń metodyki Lean występuje również nauka pracowników oparta na praktyce, podejście to umożliwia poznanie procesu, w tym działania maszyn, na każdym poziomie, włączając w ten proces informacje teoretyczne, przekazywane przez bardziej doświadczonych pracowników. Ważnym aspektem jest ciągłe zdobywanie nowych umiejętności i doświadczeń. W metodologii Lean Manufacturing istotne jest nieustanne dążenie do skrócenia działań, które nie przynoszą wartości dla przedsiębiorstwa, co za tym idzie eliminacji występujących błędów i polepszeniu jakości wytwarzanych produktów. Z założeń Lean ściśle korzysta strategia TPM, dąży do osiągnięcia równie efektownych korzyści, skupiając się na utrzymaniu niezawodności maszyn i narzędzi.
Źródło: Czerska J., Lean concept as modern company transformation approach
Czym kieruje się TPM?
TPM (Total Productive Maintenance) – podejście zakładające utrzymanie maszyn na najwyższym stopniu ich sprawności. W jego przypadku, podobnie jak w Lean Manufacturing, musimy skupić się na tym, że bez zaangażowania pracowników i ich chęci do zmian, procesy optymalizujące nie sprawdzą się najlepiej. Często jednak TPM jest błędnie sprowadzane do jednego założenia: operatorzy sami czyszczą i smarują maszyny. TPM to znacznie więcej, a wprowadzenie go wymaga dużego zaangażowania zarówno kadry kierowniczej, jak i pracowników produkcyjnych.
Szczególnie podkreślana w podejściu Total Productive Maintenanace jest świadomość pracowników, co do obecnego miejsca pracy, przyjęcie odpowiedzialności związanej z dbaniem o czystość, stan maszyn i urządzeń, jak również bezpieczeństwo swoje i współpracowników. Działania z zakresu czyszczenia i obserwacji stanu maszyn, wykonywane przez operatorów prowadzą do wydłużenia żywotności maszyn. Pamiętajmy jednak, że kluczowe w tym przypadku jest podnoszenie kwalifikacji i umiejętności specjalistów odpowiedzialnych za przypisane im zadania.
TPM jako składowa ideologii Lean Manufacturing, wykorzystuje jedną z metod pomagającą osiągnąć założenie niwelowania zbędnego ruchu. Metoda 5S, nazywana też praktykami 5S,
zakłada wprowadzenie:
• selekcji,
• systematyki,
• sprzątania,
• standaryzacji,
• samodyscypliny.
Praktyki te to zorganizowany program angażujący wszystkich pracowników do utrzymania czystych, uporządkowanych i bezpiecznych stanowisk roboczych. Jest to jedna z dróg ku pełnemu zaangażowaniu pracowników na rzecz jakości i niezawodności maszyn. Jednak pamiętajmy, że istnieją systemy, które mogą wpierać zatrudnionych w wypełnianiu zadań i utrzymywaniu procesów na wysokim poziomie kultury organizacyjnej i jakości produkcji. Większość czynności opartych o strategie TPM, może być przeprowadzona z poziomu jednostek systemów CMMS.
Jak działa CMMS?
Wdrożenie systemu CMMS to również nie małe przedsięwzięcie dla całego przedsiębiorstwa. Gwarantuje jednak automatyzację i cyfryzację działów utrzymania ruchu i produkcji oraz usprawnia działania wszystkich techników. Funkcjonalności systemu dostosowane są do każdego z pracowników, zależnie od zajmowanego stanowiska. Pozwala to szybciej i efektywniej wdrożyć się w wykorzystanie cyfrowej pomocy, co niweluje opór pracowników przed zmianą. Pamiętajmy jednak, że niezwykle ważne jest zarządzanie zmianą w przedsiębiorstwie w trakcie, jak i po wdrożeniu systemów.
Systemy CMMS udostępniają cyfrowe tablice Kaizen, dzięki czemu spełnienie założeń Lean Manufacturingu staje się łatwiejsze i szybsze. Wysyłanie zgłoszeń o zauważonych nieprawidłowościach przez pracowników, pomaga szybko reagować i wprowadzać zmiany na lepsze.
Oprócz tego możemy wyświetlać tablice Kanban, np. na telewizorach w dziale utrzymania ruchu czy na produkcji, dzięki którym mamy stały wgląd w wykonywane prace, wiemy co zostało ukończone, jakie zadania trwają, a jakie zostały zaplanowane.
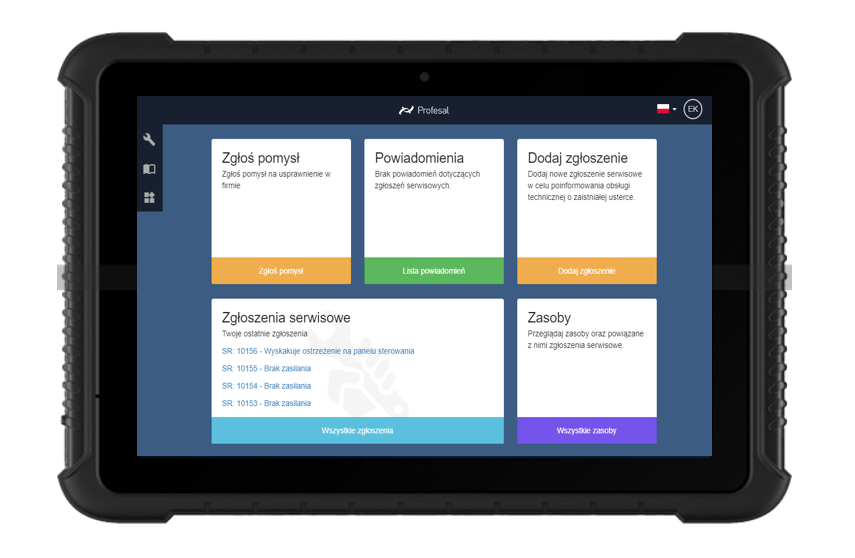
Systemy CMMS pozwalają również tworzyć przejrzysty i funkcjonalny harmonogram zadań z uwzględnieniem zajętości pracownika, matryc kompetencji i priorytetu działań. Ważna jest również możliwość tworzenia zadań okresowych, tak, aby przeglądy i działania konserwujące były wykonywane regularnie. Ten aspekt jest szczególnie istotny dla koncepcji Lean i strategii TPM, ponieważ, jak pamiętamy, obie ideologie opierają się na
ciągłym rozwoju, planowaniu działań z wyprzedzeniem.
Wydłużenie żywotności maszyn i dbanie o ich stan techniczny, jest niezwykle ważne w celu zwiększenia wydajności i sprawności całej produkcji. Kolejną funkcjonalnością systemów CMMS, która ułatwia przeprowadzanie przeglądów, wykonywanie list kontrolnych, są końcówki mobilne, dostępne dla każdego technika na telefonie lub tablecie. Zmiana papierowych list kontrolnych, na cyfrowe checklisty podpięte pod odpowiednie zadanie, ułatwia pracę i niweluje wystąpienie ewentualnych błędów czy niedociągnięć.
Podsumowanie
Stosowanie koncepcji Lean Manufacturing to sposób na tworzenie wydajnego i efektywnego przedsiębiorstwa. Strategia TPM wpływa na sprawność produkcji i niweluje nieplanowane przestoje. Systemy CMMS to narzędzie pomagające zarządzać działaniami i planować je. Jednak teraz połączmy zdobyte informacje w całość i zobaczymy, jakie wnioski ze sobą niosą…
Wartość | Lean | TPM | CMMS |
Eliminacja czynności bez wartości | Skrócenie czasu procesów | Eliminacja krótkich przestojów i biegu jałowego | Możliwość szybkiego pobierania części, dzięki kodom QR |
Zmotywowane i chętne do pracy zespoły | Angażowanie pracowników we wszelkie prace przy maszynach | Szkolenia operatorów z codziennej konserwacji zapobiegawczej | Łatwy i szybki dostęp do dokumentacji maszyn i historii napraw |
Standaryzacja działań | Przyjęcie jednej metodyki pracy niezależnie od wykonującego | Wyrobienie nawyków | Zdefiniowane proste w obsłudze listy kontrolne |
Przejrzystość działań | Organizacja pracy - przejrzysty wgląd w zaplanowane prace zespołu | Zdefiniowane i jawne odpowiedzialności produkcji i UR | Dostosowanie końcówek do stanowisk pracowników, co ułatwia przeprowadzenie zmiany w przedsiębiorstwie |
Zwiększenie jakość produkcji | Niwelowanie braków jakościowych w procesie | Stosowanie narzędzi pozwalających zachować najlepszą jakość produktu finalnego | Automatyczne powiadomienia oddziału jakości dla konkretnych maszyn na podstawie próbkowania w trakcie procesu |
Przedłużenie eksploatacji zasobów | Zniwelowanie zbędnego przetwarzania | Wprowadzenia działań prewencyjnych i predykcyjnych | Planowanie na podstawie czasu lub motogodzin/ predykcja na podstawie danych z czujników |
Zapewnienie bezpieczeństwa | Analiza, likwidacja niebezpieczeństwa lub zabezpieczanie miejsc pracy | Analiza i ciągła weryfikacja miejsc potencjalnie niebezpiecznych | Możliwość dodawania zgłoszeń bhp za pomocą końcówek mobilnych ze wszystkimi informacji oraz automatyczna analiza ryzyka |
Ciągłe doskonalenie | Ciągły rozwój - nieustanna optymalizacja procesów wewnątrz firmy | Ciągłe zaangażowanie i współpraca produkcji i utrzymania ruchu dla zwiększenie efektywności maszyn | Zgłoszenia KAIZEN pracowników oraz ciągle zwiększające swoje możliwości rozwiązanie |
Eliminowanie marnotrawstw | 7 podstawowych start - 7 Muda | Minimalizacja nieplanowanych przestojów, zmniejszenie wad oraz wypadków | Analiza procesów oraz propozycje skrócenie czasów działań utrzymania ruchu przy zwiększeniu efektywności |
Po analizie dzisiejszego artykułu możemy wyróżnić kilka zasad, które łączą te trzy skróty:
- Odzwierciedleniem 7 marnotrawstw, w TPM jest minimalizacja nieplanowanych przestojów, zmniejszenie wad oraz wypadków, uzyskane dzięki wykorzystaniu systemu CMMS (raportów, analizy czasów reakcji, całkowitych czasów awarii oraz analiz PARETO).
- Odpowiedzią na ciągły rozwój, przy nieustannej optymalizacji procesów wewnątrzfirmowych, w TPM jest ciągłe angażowanie i współpraca produkcji z UR, co prowadzi do zwiększenia efektywności maszyn, a systemy CMMS pomagają osiągnąć oczekiwane skutki, dzięki dostępności platform dla różnych zespołów o określonych funkcjonalnościach (możliwość dodawania plików, zdjęć, zgłoszeń KAIZEN, a co za tym idzie analiz przyczyn źródłowych).
- Zapowiedzią likwidacji niebezpiecznych miejsc pracy jest analiza i ciągła weryfikacja potencjalnych niebezpieczeństw, dzięki możliwości dodawania zgłoszeń BHP za pomocą platform wizualizujących wspomniane miejsca (możliwość rejestrowania zgłoszeń potencjalnie niebezpiecznych z dokładną wizualizacją miejsca wraz z określeniem jego ryzyka).
- Zniwelowanie zbędnego przetwarzania odzwierciedla w TPM wprowadzenie działań prewencyjnych i predykcyjnych, co jest możliwe przy wykorzystaniu systemu CMMS i jego funkcji wsparcia planowania prewencyjnego i predykcyjnego (planowanie na podstawie czasu lub motogodzin oraz możliwa do wprowadzenia predykcja na podstawie danych z czujników).
- Odpowiedzią na niwelowanie braków jakościowych w procesie jest stosowanie badań i narzędzi pozwalających zachować najlepszą jakość produkcji, system dla utrzymania ruchu może być również narzędziem pomocniczym dla działu jakości (dodawanie zgłoszeń do miejsc procesu produkcyjnego, mogące powodować wady będące przyczyna niezgodności próbek w czasie badan jakościowych).
- Uzyskanie przejrzystości działań, dzięki sumiennej organizacji pracy i umożliwianie wglądu w zaplanowane prace możliwe jest za pomocą przyjaznych dla użytkownika końcówek mobilnych dostępnych w systemach informatycznych (wizualizacje na telefonach czy tabelach, kalendarzy oraz planowanych dla pracownika jego zadań i obowiązków).
- Perspektywą TPM dla przejęcia jednej metodyki pracy, niezależnej od pracownika wykonującego działania, jest wyrobienie dobrych nawyków, które będą skutkować polepszeniem jakości produkcji, przy wykorzystaniu prostych w obsłudze list kontrolnych dostępnych w systemie CMMS (list dedykowanych dla Utrzymania Ruchu oraz produkcji w przypadku funkcjonowania autonomous maintenance).
- Motywowanie pracowników poprzez angażowanie ich we wszelkie prace na maszynach, realizowane jest w TPM poprzez regularne szkolenia operatorów z codziennej konserwacji zapobiegawczej, co jest jednym z głównych założeń systemu CMMS (łatwy i szybki dostęp do dokumentacji maszyn, historii napraw oraz wszelkich informacji o modernizacjach).
- Eliminowanie krótkich przestojów i biegu jałowego odpowiada na wymogi szczupłego wytwarzania - skrócenie czasu trwania procesów, uzyskane dzięki możliwości szybkiego pobierania części (znakowanych kodami QR).
Niezależnie od obranej strategii pamiętaj, że zawsze możesz skorzystać z narzędzi, które pomogą Ci wprowadzić ją w przedsiębiorstwie, jednym z nich są systemy CMMS, a my od siebie polecamy CMMS Profesal Maintenance, który dostarcza funkcjonalności pozwalające polepszyć efektywność działu utrzymania ruchu.